Meta Description:
Compare seamless and welded pipes in terms of cost, pressure capacity, corrosion resistance, and industrial use. Learn how to choose the right pipe for your project.
Introduction
In pipeline engineering, one of the most common questions from project engineers and procurement teams is:
“Should we use seamless pipes or welded pipes?”
Each option has distinct advantages and trade-offs, and your decision will affect cost, reliability, inspection requirements, and even compliance with standards such as ASME B31.3 or API 5L.
Let’s break down the key differences to help you make the right material decision.
1. Manufacturing Process
- Seamless Pipe: Made from solid round billets, heated and pierced to form a tube with no longitudinal weld.
- Welded Pipe: Produced by rolling a plate or strip and welding it longitudinally via ERW (Electric Resistance Welding), TIG, or SAW.
Result: Seamless pipes are free of weld defects but more expensive; welded pipes are cost-effective but require strict weld quality control.
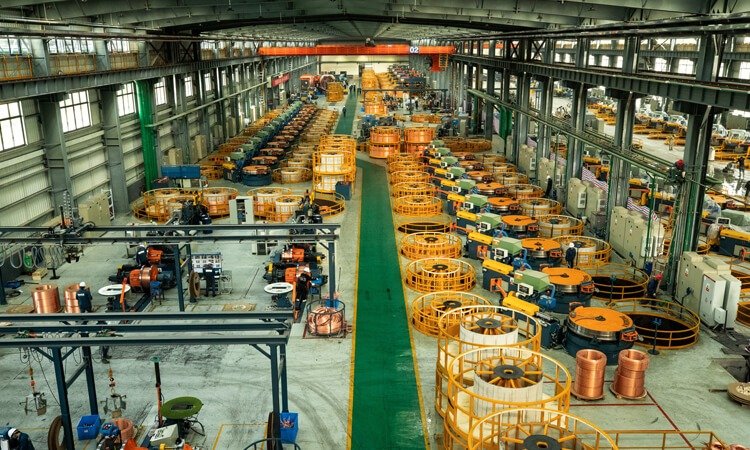
2. Mechanical Strength & Pressure Tolerance
- Seamless Pipe: Better uniformity in grain structure; withstands higher internal pressure, suitable for critical applications.
- Welded Pipe: Slightly less reliable at very high pressures due to possible weld seam discontinuities.
Standard reference:
ASME B31.3 and EN 13480 often prefer seamless for high-pressure, high-temperature, or critical service pipelines.
3. Corrosion Resistance
- Seamless Pipe: No weld seam = no heat-affected zone (HAZ), which may become a weak point for corrosion.
- Welded Pipe: Weld seam must be pickled, passivated, or annealed to restore corrosion resistance.
Note: Welded pipes are widely used in food, water, and low-pressure oil lines where corrosion risk is manageable.
4. Dimensional Range & Availability
Criteria | Seamless Pipe | Welded Pipe |
---|---|---|
OD Range | Typically 6–114 mm | Available up to 2000 mm |
Wall Thickness | Thicker walls in small diameters | Thinner walls, but large OD possible |
Lead Time | Longer, depending on billet supply | Shorter, more flexible production |
5. Cost & Application Suitability
- Seamless: Higher cost, used in boilers, superheaters, offshore, aerospace, power plants.
- Welded: Cost-effective, ideal for architectural, water distribution, food processing, general chemical use.
Industry examples:
- Power plants → Seamless
- Beverage plants → Welded
- Oil pipelines (API 5L B/X42) → Welded
- Heat exchanger U-tubes → Seamless
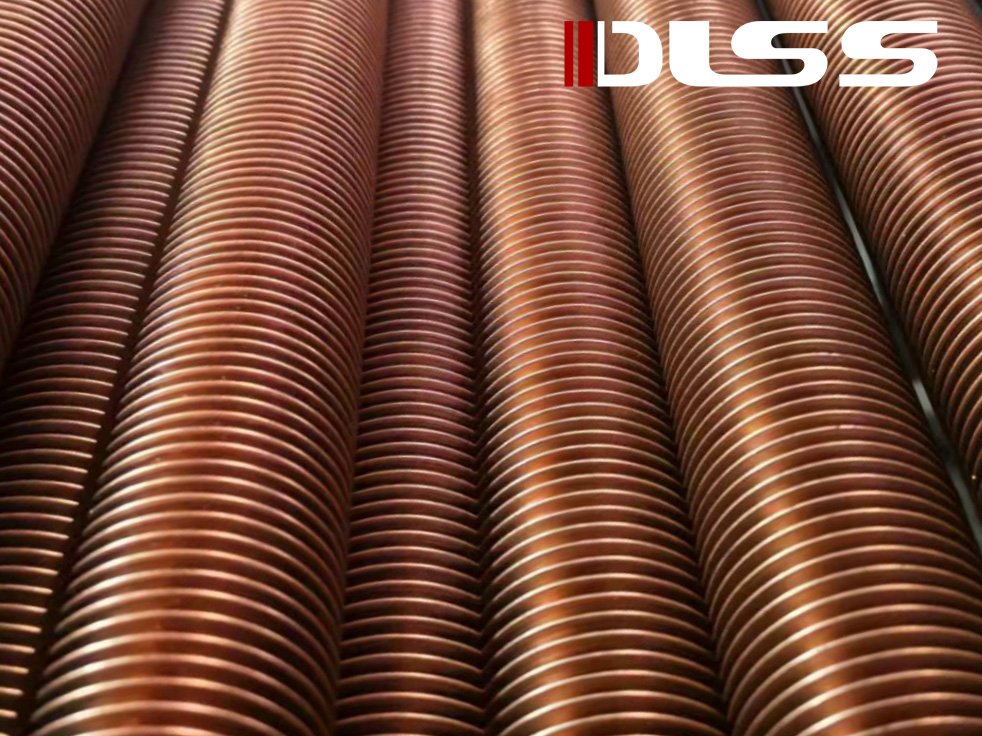
DLSS Manufacturing Capabilities
- Seamless Pipe: ASTM A312 / A213 / A269
- Welded Pipe: ASTM A249 / A358 / EN 10217-7
- Grades: TP304/304L, TP316/316L, TP321, TP347H, Duplex 2205
- Surface: Pickled, BA, EP, MP
- Testing: Hydro test, Eddy current, PMI, UT, RT (for weld seams)
Frequently Asked Questions
Q: Is seamless pipe always better than welded?
Not always. Seamless is preferred for pressure and critical service, but welded pipes are sufficient and more cost-efficient for many industrial uses.
Q: Can DLSS supply both types?
Yes, DLSS supplies both seamless and welded pipes, with full certification, surface treatment, and third-party inspection if needed.
Q: Are welded pipes allowed in oil & gas projects?
Yes. In many API 5L and offshore projects, welded pipes are allowed, especially with proven NDT records and weld seam quality.
Conclusion
Choosing between seamless and welded pipe depends on application criticality, budget, and standard compliance. DLSS helps clients make informed decisions and supplies both pipe types with strict quality control, full traceability, and reliable global delivery.
Contact DLSS
Email: info@dlsspipe.com
Website: www.dlsspipeline.com
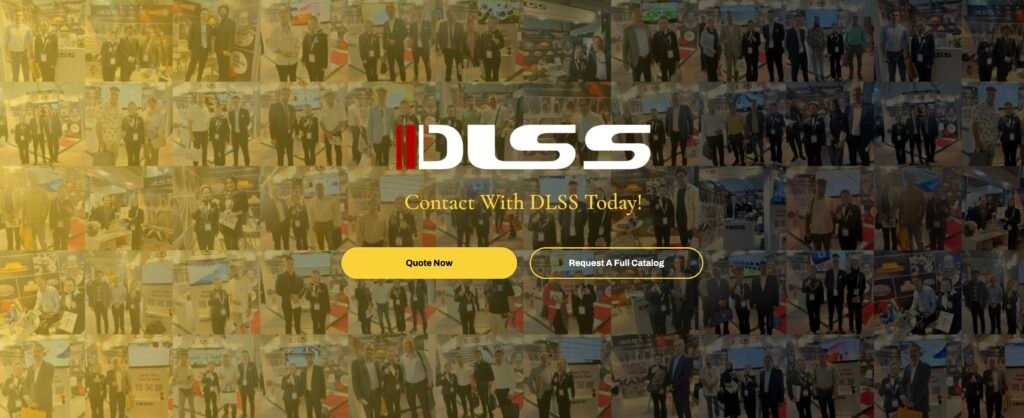