Meta Description:
Explore the most frequent defects found in stainless steel heat exchanger tubes, including pitting, thinning, and cracking. Learn how to detect and prevent these issues to extend tube service life.
Introduction
Stainless steel heat exchanger tubes play a critical role in transferring heat efficiently under corrosive and high-pressure conditions. However, defects in these tubes can lead to failures, downtime, or even safety incidents. Understanding the most common problems and their prevention measures is essential for engineers, inspectors, and plant operators.
In this guide, we highlight the top 10 most common tube defects, their causes, detection methods, and prevention strategies.
1. Pitting Corrosion
What it is: Localized corrosion that forms deep pits on the surface.
Cause: Chloride ions, stagnant fluid zones, improper passivation.
Detection: Visual inspection, penetrant testing (PT), eddy current testing (ECT).
Prevention:
- Use high-molybdenum grades like TP316L or Super Duplex
- Maintain clean flow inside tubes
- Ensure proper pickling or bright annealing
2. Wall Thinning
What it is: Gradual erosion of the inner wall, reducing tube strength.
Cause: Turbulent flow, high-velocity fluids, or abrasive particles.
Detection: Ultrasonic thickness measurement.
Prevention:
- Limit fluid velocity
- Use erosion-resistant materials
- Periodic wall thickness monitoring
3. Stress Corrosion Cracking (SCC)
What it is: Cracking caused by tensile stress and corrosive environment.
Cause: Chloride stress, welding defects, high temperatures.
Detection: Visual + dye penetrant + metallographic examination.
Prevention:
- Use Duplex or Super Duplex stainless steel
- Control welding heat input
- Post-weld heat treatment (if required)
4. Intergranular Corrosion (IGC)
What it is: Attack along grain boundaries due to chromium carbide precipitation.
Cause: Improper heat treatment or excessive welding heat.
Detection: ASTM A262 Practice E test.
Prevention:
- Use low carbon grades (L-grade, e.g., TP316L)
- Avoid long exposure in 500–800°C range
5. Denting or Ovality
What it is: Deformation in tube shape affecting bundle tightness.
Cause: Poor handling during transport or installation.
Detection: Dimensional inspection with caliper or ovality gauges.
Prevention:
- Use wooden separators in packing
- Handle tubes with care
- Specify ovality tolerance in purchase spec
6. Tube Leaks
What it is: Perforation or joint failure resulting in fluid loss.
Cause: Corrosion, pitting, improper expansion at tube sheets.
Detection: Hydrostatic or pneumatic testing.
Prevention:
- Use proper tube-to-tube-sheet welding or rolling
- Select corrosion-resistant alloys
- Routine pressure testing
7. Cracking at U-Bends
What it is: Fracture occurring in the bend zone of U-bend tubes.
Cause: Residual stress, improper bending radius, or work hardening.
Detection: Visual inspection and eddy current test at bends.
Prevention:
- Apply stress-relieving heat treatment
- Use CNC bending machines
- Ensure proper annealing before bending
8. Surface Contamination or Discoloration
What it is: Surface rust, oil, or heat tint compromising corrosion resistance.
Cause: Improper pickling, dirty environments, or welding heat.
Detection: Visual inspection or wipe test.
Prevention:
- Apply full pickling + passivation
- Store tubes in dry, clean conditions
- Use protective end caps
9. Weld Seam Defects (for welded tubes)
What it is: Incomplete penetration, porosity, or slag in welded zone.
Cause: Poor welding control or incorrect filler material.
Detection: Radiography (RT), ultrasonic (UT), or dye penetrant test.
Prevention:
- Use seamless tubes or certified ERW/HF welded tubes
- Perform post-weld inspection
- Choose experienced welders and automated machines
10. Microstructural Inconsistencies
What it is: Variability in grain size, ferrite content, or delta phase in Duplex steels.
Cause: Improper solution annealing or poor alloy control.
Detection: Metallographic analysis or ferrite scope.
Prevention:
- Specify solution annealing with certified temperatures
- Perform ferrite content control (20–35% for Duplex)
- Use EN10204 3.1 or 3.2 certificate with heat treatment data
Conclusion
Defects in stainless steel heat exchanger tubes can significantly impact system efficiency, safety, and longevity. By understanding these common issues and applying the right manufacturing and inspection controls, failures can be avoided and service life extended.
DLSS follows strict quality procedures, including:
- 100% Hydro and Eddy Current testing
- Ferrite and grain size control
- Proper stress relief for U-bends
- Certified packaging and documentation
- Compliance with ASTM A213, A789, B111, and ASME codes
Keywords for SEO
heat exchanger tube defects, pitting in stainless steel tube, SCC in heat exchanger piping, ultrasonic thickness tube test, ASTM A213 tube inspection, U-bend cracking prevention, pickling vs bright annealed tube, TP316L corrosion failure, Duplex tube grain control, how to detect tube leaks
Need Technical Support or Custom Inspection Plans?
DLSS helps customers reduce failure risks by providing tested, certified, and traceable stainless steel tubes for critical applications worldwide.
Contact us now:
Email: info@dlsspipe.com
Website: www.dlsspipeline.com
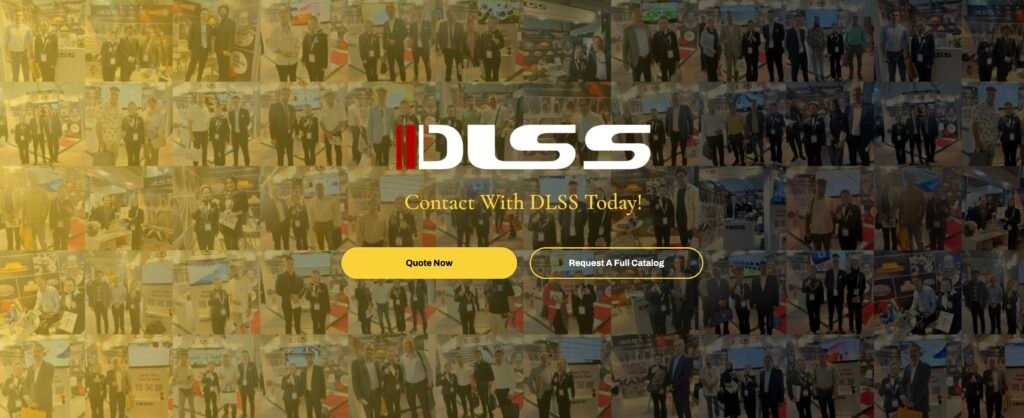