Meta Description:
Discover why grain size matters in stainless steel tubing and how DLSS ensures optimal grain structure through precise heat treatment, testing, and quality control.
Introduction
Grain size in stainless steel is more than just a microscopic characteristic—it directly affects mechanical strength, corrosion resistance, formability, and creep performance.
For critical applications such as heat exchangers, nuclear power, and chemical processing, maintaining the correct grain size (typically ASTM No. 5 to No. 8) is a specification requirement and a quality benchmark.
At DLSS, we take grain size control seriously—integrating it into our heat treatment programs, testing protocols, and material traceability system.
1. Why Grain Size Matters in Stainless Steel Tubes
Grain size impacts austenitic stainless steel in the following ways:
- Finer grains (No. 7–8):
- Better ductility and formability
- Enhanced resistance to intergranular corrosion
- Preferred for U-bend tubes, instrumentation tubing, nuclear heat exchangers
- Coarse grains (No. 3–4):
- Higher tensile strength
- Lower ductility
- Susceptible to sensitization and stress corrosion cracking in weld heat-affected zones (HAZ)
Reference: ASTM E112 – Standard Test Methods for Determining Average Grain Size
2. Industry Standards & Customer Requirements
Grain size is commonly referenced in:
- ASTM A213 / A269 (Seamless and welded tubes for heat exchangers and condensers)
- EN 10216-5 (For pressure purpose stainless tubes)
- EDF RCC-M / ASME Section III (Nuclear industry specifications)
- Client TDCs from power, chemical, and desalination projects
Typical required range: ASTM No. 5–8 (with average size controlled and documented)
3. How DLSS Controls Grain Size
A. Solution Annealing Parameters
- Conducted at 1050–1150°C, holding time adjusted based on wall thickness and alloy type
- Rapid quenching (water or inert air) prevents carbide precipitation and grain growth
- Furnace temperature and cycle data fully recorded
B. Material-Specific Programs
- TP316L, TP321, TP347H: Precise time-at-temp control to prevent coarse grains
- Nickel alloys (Incoloy 825, Alloy 625): Dual-phase structure stabilization
- Duplex grades (S31803, S32750): Ferrite-austenite balance with fine grain uniformity
C. Post-Bending Heat Treatment for U-Tubes
- Re-annealing after U-bending restores original grain size
- Grain structure in the bend area is evaluated using etched samples
4. Grain Size Testing at DLSS
- Standard: ASTM E112 (Comparison and Intercept Methods)
- Frequency: Per heat batch and every lot for critical projects
- Tools: High-magnification optical microscope with calibrated grain charts
- Optional: Microstructure photo archive and digital reports for clients
Learn more about grain size testing: NDT Resource Center – Microstructure Testing
5. Real-World Example:
Project: TP316L BA Seamless Tubes for Pharmaceutical Condenser
Issue: Client specified minimum ASTM No. 6 grain size
DLSS Solution:
- Adjusted annealing dwell time + water quench
- Conducted grain size testing and provided photo evidence
- Third-party inspection (SGS) verified compliance
- Delivered tubes passed visual, hardness, PMI, and grain size requirements
Result: DLSS approved as long-term supplier for GMP-grade stainless tubing.
6. Summary Table – DLSS Grain Size Control Scope
Grade | Target Grain Size (ASTM No.) | Process Control | Notes |
---|---|---|---|
TP304L / TP316L | No. 6–8 | Solution annealing + water quench | For general & pharma applications |
TP321 / TP347H | No. 5–7 | Stabilized annealing | For high-temp, creep-resistant usage |
S31803 / S32750 | Duplex structure, fine grain | Balanced heat cycle | Avoid intermetallic phases |
Incoloy 825 | No. 5–7 | Controlled cooling | For chemical & H₂SO₄ service |
Conclusion
Grain size control is an essential part of stainless steel tube manufacturing—particularly for demanding industries that require formability, corrosion resistance, and thermal stability.
DLSS integrates grain size verification into our heat treatment, testing, and documentation process, ensuring every tube meets your performance expectations and project specifications.
Contact DLSS
Email: info@dlsspipe.com
Website: www.dlsspipeline.com
Need a stainless tube supplier who understands the details that matter? DLSS delivers more than just tubes—we deliver performance you can verify.
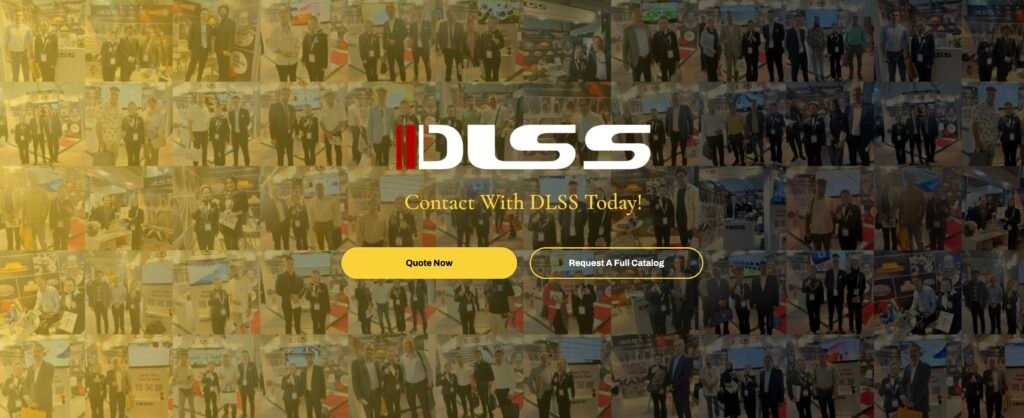