Meta Description:
Discover what electropolished (EP) stainless steel tubing is, how it’s made, and where it’s used. Ideal for pharmaceutical, semiconductor, and ultra-high-purity industries requiring extreme surface cleanliness and corrosion resistance.
Introduction
In industries where surface cleanliness, corrosion resistance, and bacterial control are critical, standard stainless steel tubing may not be enough. That’s where Electropolished (EP) Tubing comes in.
Used in biotech, pharma, semiconductor, and ultra-pure water systems, electropolished tubing delivers a smooth, passive, contamination-resistant internal surface that outperforms mechanically polished finishes.
1. What is Electropolished (EP) Tubing?
Electropolishing is a controlled electrochemical process that removes a thin layer of material from the stainless steel surface, improving:
- Surface roughness (Ra)
- Corrosion resistance
- Cleanability
The process creates a chromium-rich passive layer, free from embedded contaminants or micro-crevices that harbor bacteria.
2. How is EP Tubing Made?
Production Steps:
- Cold drawn or welded tube
- Bright annealing
- Initial mechanical polish (optional)
- Acid cleaning and pre-treatment
- Electropolishing in acid bath under DC current
- Neutralization and rinsing
- Ultrapure water cleaning
- Class 100 cleanroom packaging (optional)
3. Surface Roughness (Ra) Comparison
Finish Type | Typical Ra (μm) |
---|---|
Mill Finish | 0.8 – 1.2 |
Mechanically Polished | 0.4 – 0.8 |
Electropolished (EP) | 0.2 – 0.4 |
Ultra EP | ≤ 0.1 |
EP tubes may also meet ASME BPE, SEMI F20, or DIN 11866 requirements for UHP systems.
4. Applications of Electropolished Tubing
Industry | Application Example | Recommended Grades |
---|---|---|
Pharmaceutical | WFI loops, injection systems | TP316L EP, 1.4435 |
Biotechnology | Fermentation, sterile filtration | TP316L, 1.4404 |
Semiconductor | UHP chemical transport, gas distribution | TP316L Ultra EP |
Food & Beverage | Dairy and beverage processing | TP304L / TP316L EP |
Laboratory & R&D | High-purity water systems | 316L BA + EP |
Medical Devices | Implantable equipment tubing | Custom electropolished |
Learn more: SEMI F20 Standard Overview
5. Key Benefits of Electropolished Tubes
- Superior corrosion resistance (especially in CIP/SIP systems)
- Reduced biofilm formation
- Fewer particles and lower TOC
- Improved flow characteristics
- Longer equipment lifespan
6. DLSS Electropolished Tube Capabilities
- Size Range: OD 6 – 101.6 mm
- Materials: TP316L (1.4404), TP304L, 1.4435
- Standards: ASTM A270 / A269 + ASME BPE
- Ra Options: ≤ 0.4 μm standard, ≤ 0.25 μm optional
- Testing:
- Surface roughness (Ra) reports
- PMI, hydro, ET
- Passivation report (per ASTM A967)
Packaging: Double PE bag + cleanroom polybag sealing. Nitrogen-purged packaging optional.
FAQs
Q1: Is EP tubing suitable for welding?
Yes, but welds must also be electropolished or passivated to maintain surface integrity.
Q2: Can EP tubes be used in vacuum or gas applications?
Absolutely. EP finish helps minimize outgassing, ideal for UHV/clean gas delivery.
Q3: Is EP necessary if using TP316L?
Material alone isn’t enough for hygiene-sensitive systems—surface finish is key.
Q4: What’s the shelf life of EP tubes?
If properly sealed and stored, EP tubes can retain cleanliness for years, especially in nitrogen-purged packaging.
Conclusion
Electropolished tubing is the gold standard for hygienic, ultra-clean, and corrosion-sensitive applications. DLSS provides EP tubing with world-class surface finish, full testing reports, and compliant packaging—meeting the most demanding purity standards in the market.
Contact DLSS
Email: info@dlsspipe.com
Website: www.dlsspipeline.com
Need electropolished tubing for your clean process system? Contact DLSS for expert consultation and quotation.
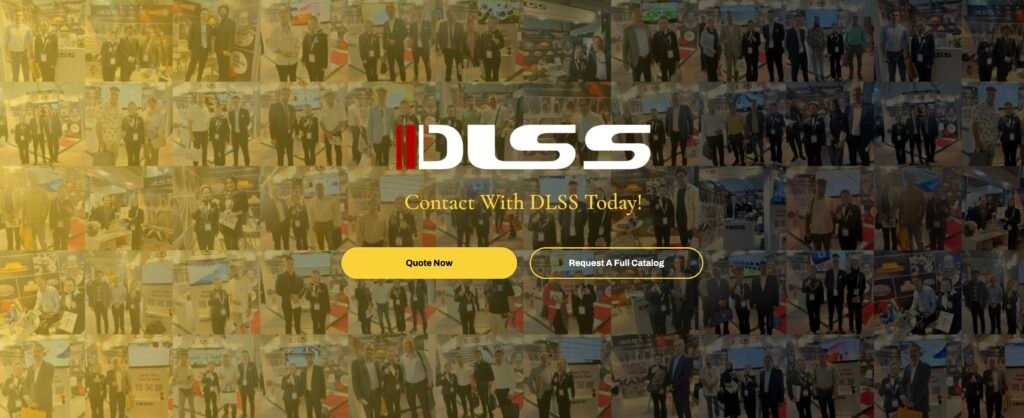