Meta Description:
Explore the 10 most common materials used in pipeline engineering, from stainless steel and carbon steel to exotic alloys. Understand their pros, cons, and applications across industries.
Introduction
Choosing the right material is one of the most critical decisions in pipeline engineering. The material affects not only the strength, corrosion resistance, and temperature tolerance of the pipeline but also impacts cost, lifespan, and safety.
Whether you’re designing for oil & gas, chemical processing, power plants, or marine environments, here are the top 10 materials used in industrial piping systems—and what makes each one ideal for certain conditions.
1. ASTM A312 TP316L – Low Carbon Stainless Steel
- Key Properties: Excellent corrosion resistance, especially in chloride and acidic environments
- Applications: Food & beverage, pharmaceuticals, offshore platforms, heat exchangers
- Standards: ASTM A312 / A213, EN 10216-5
Why it’s used: Its low carbon content reduces carbide precipitation during welding, improving long-term corrosion resistance.
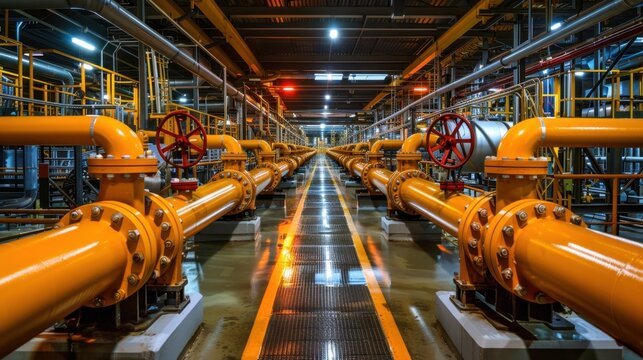
2. ASTM A312 TP304/304L – General Purpose Stainless Steel
- Key Properties: Good weldability and corrosion resistance
- Applications: Water systems, dairy processing, general industrial use
- Standards: ASTM A312, ASME B36.10
Why it’s used: Economical and versatile; widely available and easy to form.
3. ASTM A213 TP321 / TP347 – Stabilized Stainless Steels
- Key Properties: Prevents intergranular corrosion at high temperatures
- Applications: Heat exchangers, steam pipes, thermal processing systems
- Standards: ASTM A213, EN ISO 1127
Why it’s used: Titanium or niobium stabilization allows higher thermal performance.
4. ASTM A789 / A790 S31803 – Duplex Stainless Steel
- Key Properties: Twice the strength of 304/316, high chloride pitting resistance
- Applications: Offshore oil rigs, desalination plants, aggressive fluid handling
- Standards: ASTM A790, EN 10216-5
Why it’s used: Ideal when high strength and corrosion resistance are both needed.
5. ASTM A106 Gr B – Seamless Carbon Steel Pipe
- Key Properties: High strength, high temperature tolerance
- Applications: Steam pipelines, power generation, oil transport
- Standards: ASTM A106, ASME B36.10
Why it’s used: A cost-effective choice for high-temperature, non-corrosive environments.
6. ASTM B111 C44300 (Admiralty Brass)
- Key Properties: Excellent resistance to dezincification, erosion
- Applications: Condensers, heat exchangers, refinery cooling systems
- Standards: ASTM B111
Why it’s used: Copper alloy that performs well in seawater and brine environments.
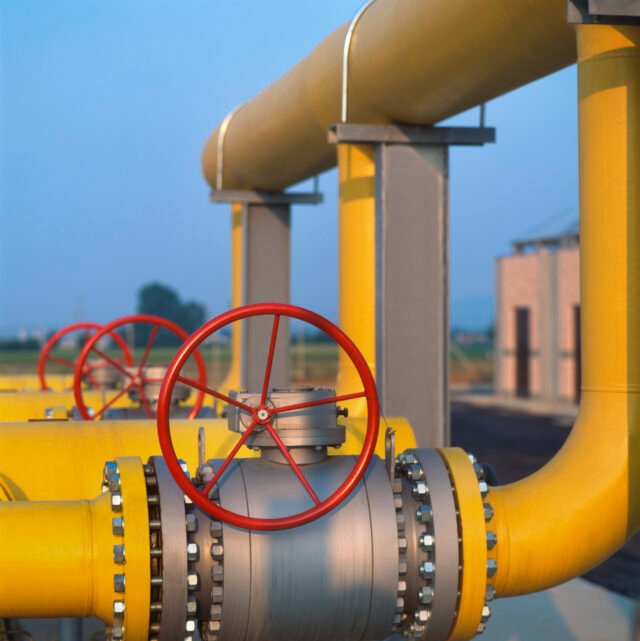
7. ASTM B163 / B423 UNS N08825 (Incoloy 825)
- Key Properties: Superior resistance to sulfuric and phosphoric acid
- Applications: Chemical reactors, pollution control, acid handling systems
- Standards: ASTM B163, B423
Why it’s used: Preferred for highly corrosive, acidic process environments.
8. ASTM B622 UNS N10276 (Hastelloy C276)
- Key Properties: Exceptional resistance to strong oxidizers and reducers
- Applications: Waste treatment, biofuels, fertilizer production
- Standards: ASTM B622
Why it’s used: Ideal for extreme chemical process conditions.
9. ASTM A335 P22 – Chrome-Moly Alloy Steel
- Key Properties: High creep strength at elevated temperatures
- Applications: Power station piping, petrochemical high-pressure lines
- Standards: ASTM A335
Why it’s used: Supports extreme thermal and mechanical stress.
10. EN 1.4539 / ASTM A312 904L – Super Austenitic Stainless Steel
- Key Properties: High nickel content, excellent corrosion and acid resistance
- Applications: Seawater systems, sulfuric acid plants, marine industry
- Standards: ASTM A312, EN 10216-5
Why it’s used: Combines corrosion performance of high-end alloys with stainless steel workability.
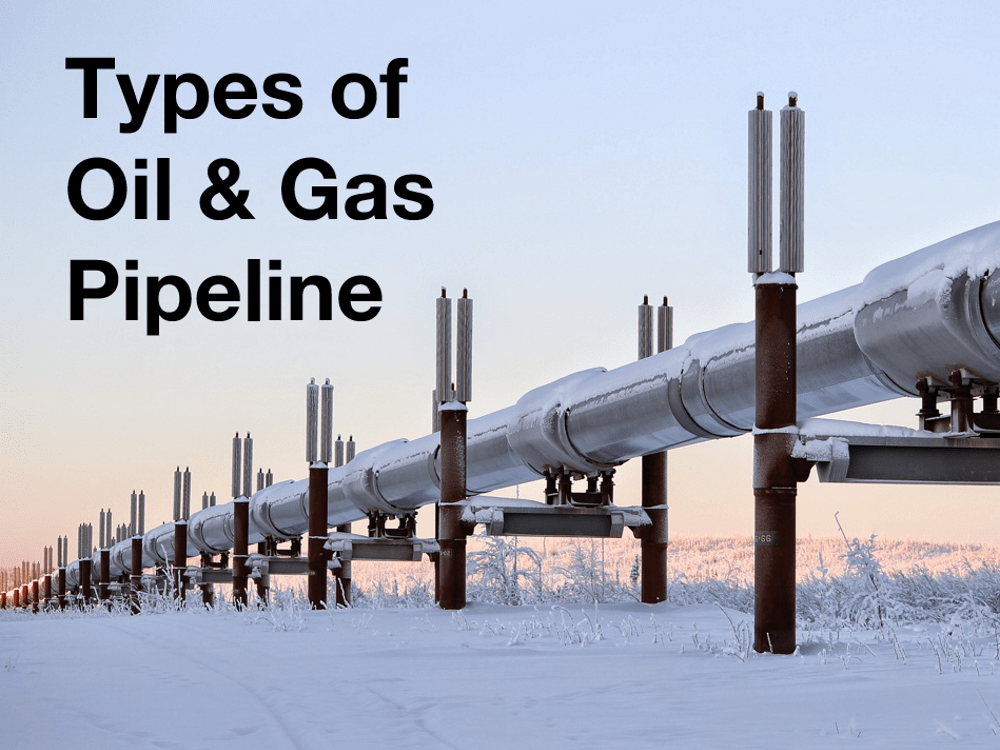
Frequently Asked Questions (FAQs)
Q1: How do I choose the right piping material for my project?
Material selection depends on several factors, including operating pressure and temperature, corrosiveness of the fluid, mechanical stress, and regulatory standards (e.g., NACE MR0175, ASME B31.3). Contact DLSS for material compatibility assessments based on your design conditions.
Q2: What’s the main difference between TP304 and TP316 stainless steel?
TP316 contains molybdenum, which significantly improves corrosion resistance, especially in chloride-rich environments like marine or food processing. TP304 is more cost-effective and used in less aggressive media.
Q3: Can DLSS supply mixed-material packages for large industrial projects?
Yes. DLSS supports project-based consolidated delivery of stainless steel pipes, fittings, and flanges in multiple grades, ensuring standard compatibility and streamlined logistics.
Q4: What is the benefit of using Duplex stainless steel over TP316L?
Duplex S31803 offers double the yield strength, better stress corrosion cracking resistance, and longer service life in aggressive or high-pressure applications. It is ideal for offshore, desalination, and oil refining.
Q5: What standards does DLSS follow to ensure material quality?
We manufacture and supply in compliance with:
- ASTM A312 / A213 / B111 / B622
- EN 10216-5 / EN 10204 3.1 / 3.2
- ASME B36.10 / B16.5 / B16.9
- NACE MR0175 (on request)
DLSS also supports third-party inspections by SGS, BV, TUV, and customer-appointed agencies.
Conclusion
Pipeline engineers must carefully match material to fluid type, temperature, pressure, and corrosive risks. Whether you’re working on an industrial boiler, an offshore platform, or a sanitary processing line, the right material means safety, efficiency, and longevity.
DLSS offers a wide selection of certified materials, with global project delivery, including full documentation and third-party inspection.
Contact DLSS
Email: info@dlsspipe.com
Website: www.dlsspipeline.com
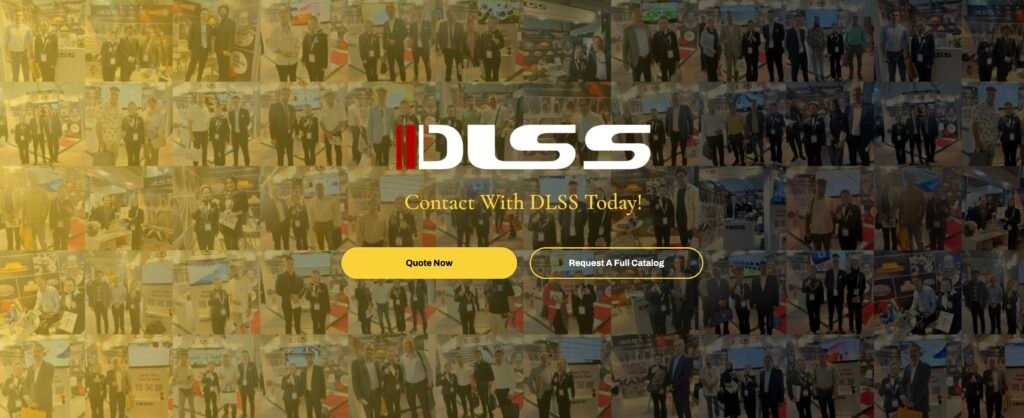