Meta Description:
Need the right tubes for refinery heaters, boilers, or exchangers in Latin America? This guide explains how to choose the best stainless and alloy grades for performance and corrosion resistance.
Introduction
Refinery operations across South America—whether in Argentina’s Mendoza, Brazil’s São Paulo, or Chile’s Bío-Bío region—require tubing that can handle high temperature, pressure, and aggressive process fluids.
The choice of tube material directly impacts the safety, efficiency, and life cycle cost of refinery units like:
- Hydrotreaters
- Furnace coils
- Heat exchangers
- Steam reformers
- Desalters and fractionators
In this article, we explain the key factors in material selection and provide a practical guide to choosing the right stainless steel and alloy tubes for refinery environments.
Key Considerations for Refinery Tubes
When selecting tubes for refineries, engineers must consider:
- Operating temperature (up to 1000°C for furnace tubes)
- Fluid composition (sour gas, chlorides, sulfur compounds)
- Coking resistance (for hydrocarbon service)
- Weldability and fabrication
- Corrosion-fatigue resistance (due to thermal cycles)
- Standards and compliance (ASTM, ASME, ISO, NACE)
Common Tube Materials for Refineries
Material Grade | Typical Application | Strengths |
---|---|---|
TP316L | Water service, condensers | General corrosion resistance, easy to weld |
TP321 / TP347H | Furnace and superheater tubes | High-temp oxidation resistance, stabilized grades |
Alloy 800H/HT | Steam reformers, ethylene units | Excellent creep strength, carburization resistant |
Incoloy 825 | Sour service exchangers | Acid and chloride resistance, NACE-compliant |
Alloy 625 | Furnace coils, H₂S-rich services | High strength + superior corrosion resistance |
All materials can be provided by DLSS with pickled, bright annealed, or electropolished finishes, as per project needs.
International and South American Standards
DLSS supplies refinery tubing according to:
- ASTM A213 / A312 / B407 / B423
- ASME Boiler & Pressure Vessel Code (BPVC)
- NACE MR0175 / ISO 15156 for sour service
- EN 10216 and DIN standards (on request)
We also meet project-specific norms set by South American clients such as YPF (Argentina), Petrobras (Brazil), and Repsol Peru.
Real-World Example: Argentina Refinery Upgrade
In a recent project in Argentina, DLSS supplied TP347H tubes with 3.2 certification for a high-temperature gas reforming unit. The tubes were:
- ID cleaned and pickled
- 100% PMI and eddy current tested
- Delivered with full welding recommendations
Client feedback: reduced coking rates, improved heat transfer, and smooth installation with local fabrication teams.
Value-Added Services from DLSS
We don’t just supply tubes—we support refinery projects from design to delivery:
- Custom lengths and bending
- NDE options: UT, EC, PT, RT
- Surface protection with end caps + nitrogen purging
- Third-party inspection (SGS, BV, TÜV)
- On-site technical assistance (remote or bilingual)
DLSS has deep experience working with Spanish-speaking engineering teams and can provide documentation in English or Spanish upon request.
Conclusion
Choosing the right tubes for refinery applications in South America means balancing resistance, reliability, and regulation. DLSS offers high-grade stainless steel and nickel alloy tubes that meet or exceed global and regional requirements.
If you’re building, upgrading, or maintaining refinery units across Latin America, we’re here to help.
Contact DLSS
Email: info@dlsspipe.com
Website: www.dlsspipeline.com
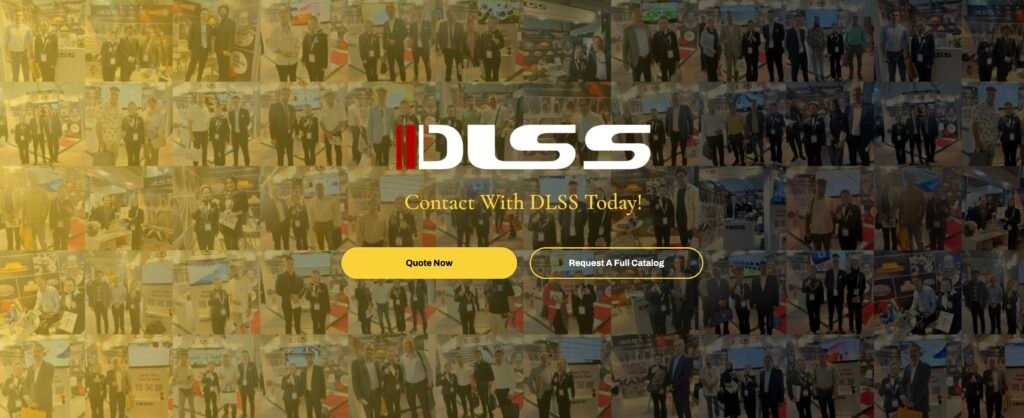